Recently, surface materials for custom home decor have expanded to include options like melamine deep texture, melamine high gloss, UV high gloss, UV matte, PVC film, and PET film. These stylish surfaces are prevalent in custom home furnishings, but during cutting, edge banding, drilling, and grooving, panels often encounter friction, which can lead to scratches and reduce final product quality. To protect these surfaces, many manufacturers use PE protective films. However, the variety of surface materials means that finding the right type of protective film is essential to achieve high-quality results. This study explores how different PE protective films perform on various surfaces to help manufacturers select the best option.
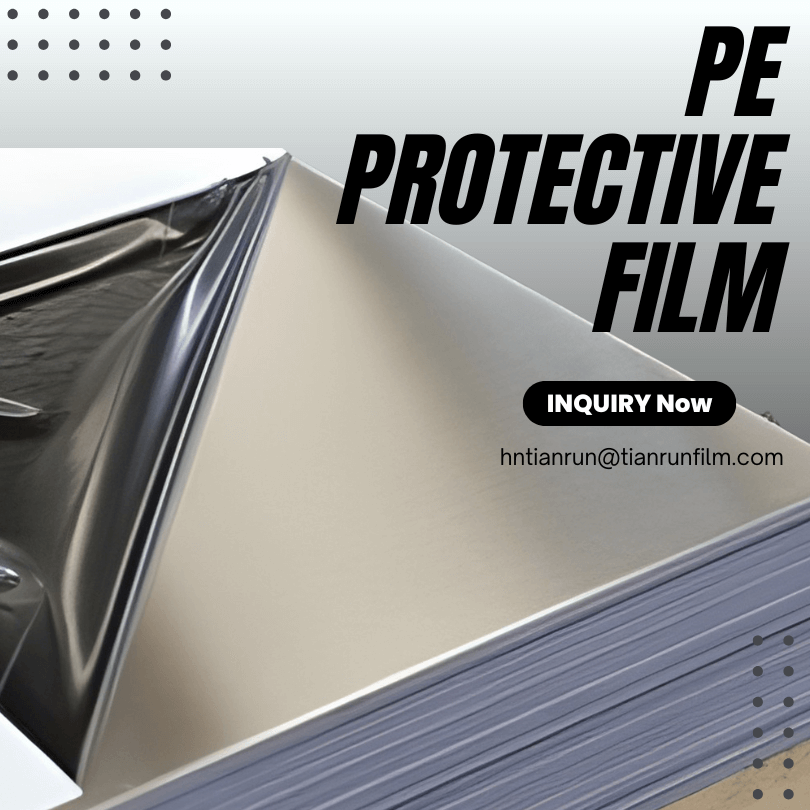
Key Steps and Testing of Protective Films
The experiment covered each processing stage, from applying a protective film to the final product to using standard and modified PE films to test film compatibility with different surfaces.
- Film Application: PE protective films were applied to each panel surface. Shallow texture panels like melamine high gloss, UV high gloss, UV matte, PVC shallow texture, and PET showed strong compatibility with over 90% pass rates for standard and 100% for modified films. Deep textures like melamine and PVC initially showed poor performance with standard films (0% pass rate) but improved with modified PE films, with pass rates of 100% for melamine deep texture and 40% for PVC deep texture.
- Cutting: Panels were cut into specified sizes. Shallow texture panels maintained a 100% pass rate with both film types, while melamine deep texture achieved 95% with modified film, PVC deep texture 86% with modified film, and 64% with standard film.
- Edge Banding: Each panel received a PVC edge band. Shallow-texture panels performed well, with a 100% pass rate, while melamine deep texture achieved 92% and PVC deep texture reached 81%.
- Drilling: Drilling tests showed that shallow texture panels remained at a 100% pass rate. Melamine deep texture had a 92% pass rate, while PVC deep texture reached 71%.
- Grooving: U-shaped grooves were milled along the thickness of the panels. Shallow texture panels again achieved a 100% pass rate, melamine deep texture 92%, and PVC deep texture 64%.
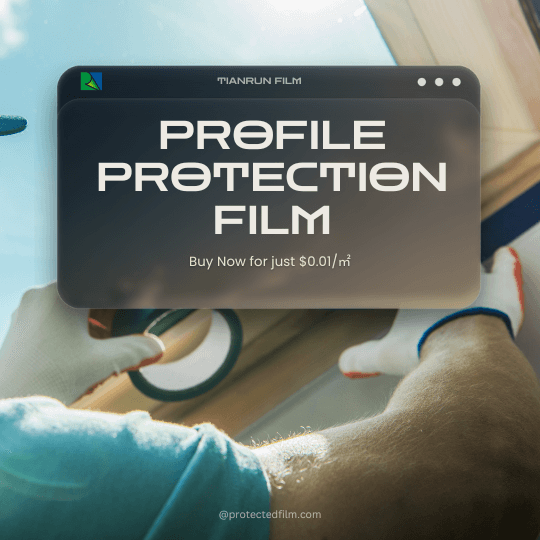
Test Results and Protective Film Suitability
Performance across different tests is summarized as follows:
- Shallow Texture Panels: Panels with melamine high gloss, UV high gloss, UV matte, PVC shallow texture, and PET finishes achieved consistently high performance with both standard and modified PE films, with no issues of peeling or film damage throughout processing.
- Deep Texture Panels: For melamine deep texture panels, modified PE film provided excellent protection with 100% pass rates in application and cutting and approximately 92% in edge banding, drilling, and grooving. PVC deep texture saw improvement with modified PE film in the application stage, reaching a 40% pass rate and improved pass rates in cutting (86%), edge banding (81%), drilling (71%), and grooving (64%).
Conclusions and Recommendations
The results suggest that shallow texture panels are well-suited for standard PE films, especially with a recommended thickness of 50-60 μm and peel strength between 28-96 N/m. This combination can preserve surface quality while preventing adhesive residue. For melamine deep texture panels, a high-strength, flexible modified PE film is recommended for best results. The tested films didn’t fully meet protection requirements for PVC deep texture panels, indicating the need for further research to find an ideal protective film solution.
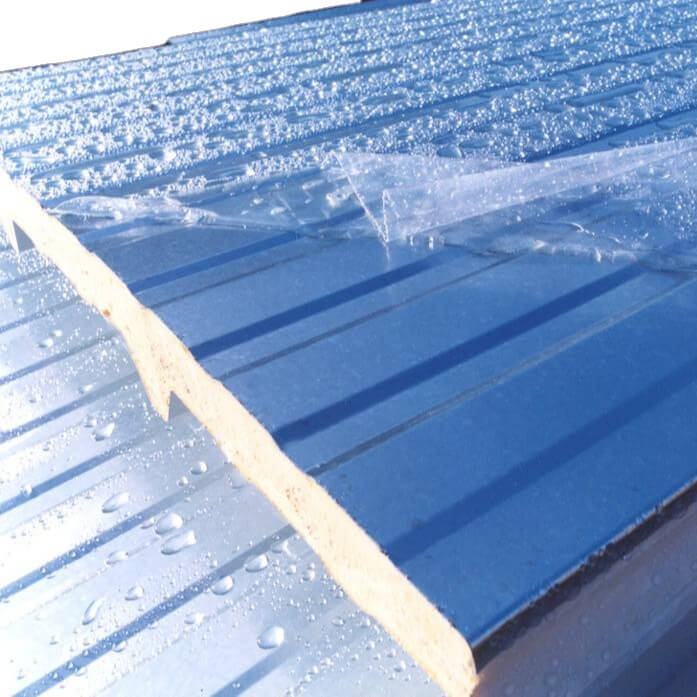