Polyethylene protective film is the world’s most concise polymer organic compound, but it is also a widely used polymer material. PE protective film is based on special polyethylene (PE) plastic film, according to the different densities, can be divided into high-density polyethylene protective film and medium-density polyethylene PE protective film is the advantage of the protected products in the process of production, processing, transportation, storage and use of the product is not contaminated, corrosion and scratches, to protect the original smooth surface, thereby improving product quality and market competitiveness. The advantage of the protective film is that the protected products will not be contaminated, corrupted, or scratched during production, processing, transportation, storage, and use, and the original smooth surface will be protected to improve the quality of products and market competitiveness.
The use of polyethylene protective film.
1. Hardware industry: Computer chassis, galvanized sheet stamping, aluminum, stainless steel, titanium, plastics and steel, glass, solar panels, etc.
2. Optoelectronic industry: Liquid crystal display, backlight, light-emitting film, membrane switch, cell phone screen, etc.
3. Plastic industry: ABS, PP injection molding products, PVC boards, acrylic boards, instruments, meters, plastic lenses, spray paint surface protection, etc.
4. Printing industry: PVC, PC board, aluminum plate, etc. PVC, PC board, aluminum, film, and other printed nameplate surface protection.
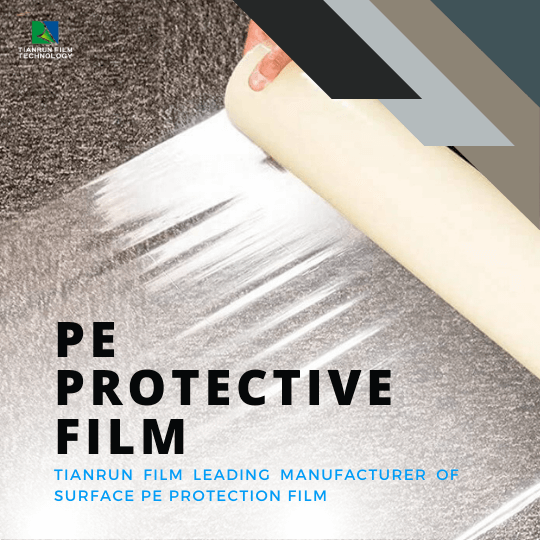
The whole production process of polyethylene protective film.
The protective film’s production process is intended to be of high quality. PE protective film molding methods are many. Three of the more common are casting, extrusion, and blow molding. The production process breakdown can be divided into blown film, coating, printing, inspection, rewinding, slitting, and packaging. The processes in each process are different, and each method is not indispensable.
Blown Film.
Blown film is plastic that is melted in the extruder and extruded through the ring, which dies into a film tube. Compressed air blows, cools, and shapes the film.
Coating.
The adhesive is prepared according to the polyethylene protective film’s specifications, model, and applicable products. Then, a coating machine evenly coats the adhesive on the substrate.
Printing.
In a gravure printing press, the printing plate is immersed in an ink cartridge, the ink is removed from the non-engraved portion of the plate with a squeegee, and the ink is transferred to the printed substrate under an embossing rubber roller.
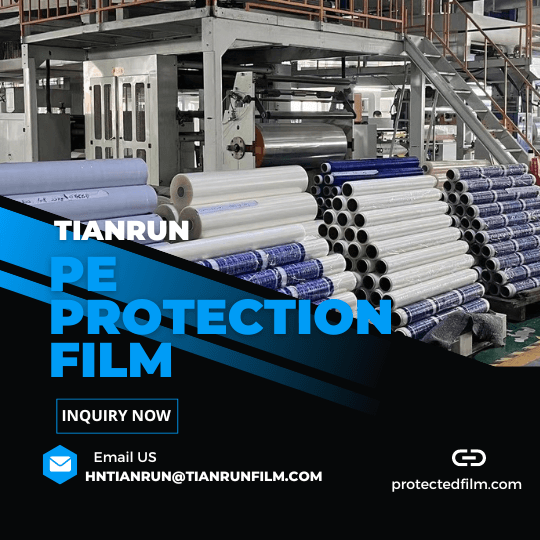
Testing.
A quality inspector will conduct product quality inspections during the production process of PE protective film, such as batching, film blowing, printing, coating, etc.
Rewinding: Semi-finished products are rewound on the inspection machine.
Semi-finished products are rewound on the inspection machine. Suppose the shape, size, and color error between the pattern fed back by the sensor and the standard sample inputted into the computer is out of a particular range. In that case, the inspection machine will automatically stop the inspection. The inspection process reduces post-processing spreading and improves product quality.
Slitting.
The slitting process divides large-size rolls of film into desired sizes. With the increasing use of automated packaging equipment, more and more rolls of film are being delivered from the factory.
Packaging.
The inspected and cut PE film products are transported to the packaging machine for packaging.